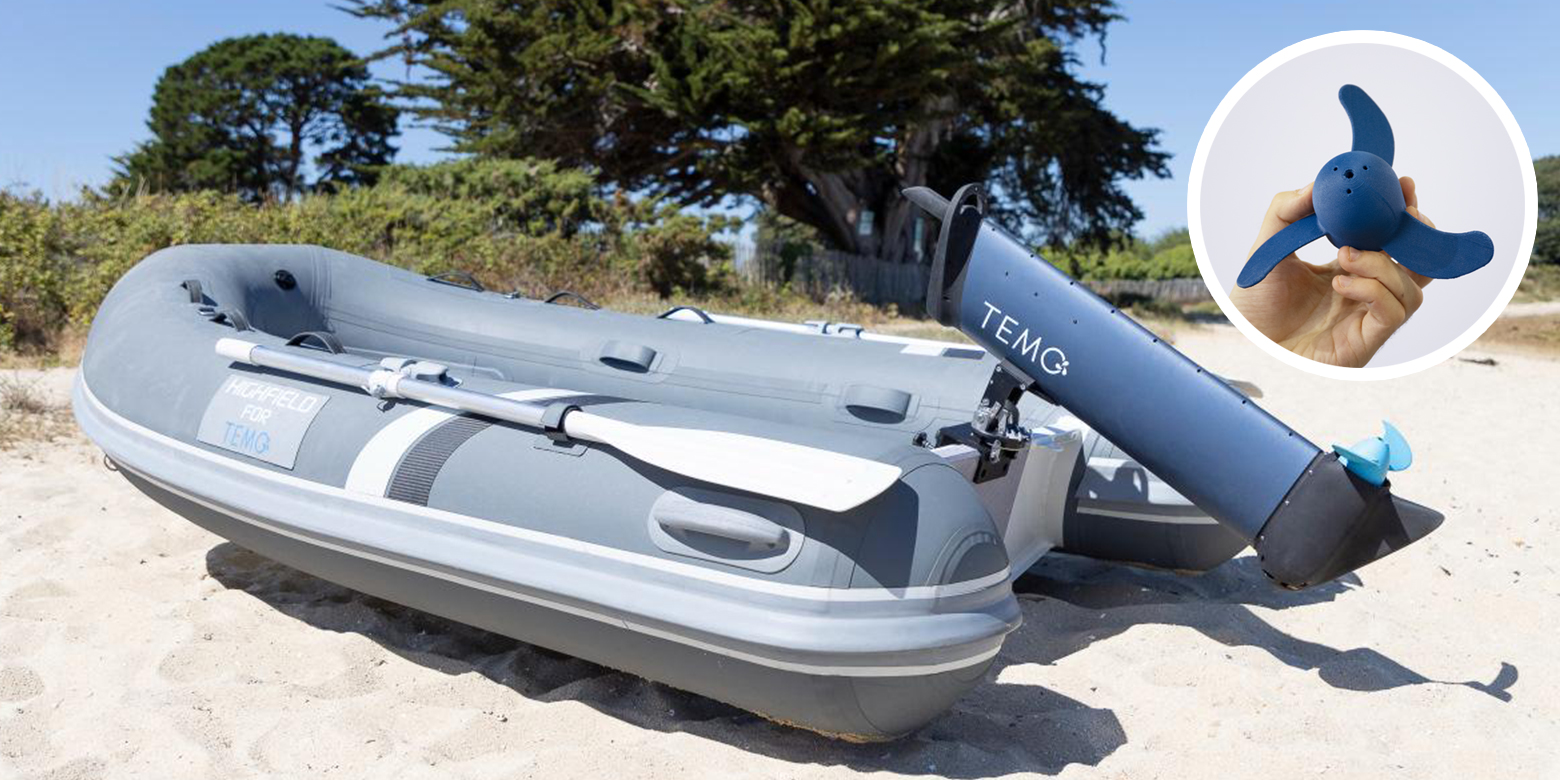
Functional prototype of propeller for outboard electric motors
It's the right time to choose to take a pleasant ride with your own tender, perhaps powered by an electric outboard. The advantage is not only economic, due to zero maintenance and lower recharging costs compared to fuel. With an electric outboard you can move silently and in a sustainable way, reducing noise and environmental pollution.
Tender boats, also known as service boats, play an essential role in the maritime industry, providing logistic support and transportation for passengers or crew members between the mainland and the main vessel.
One of the main challenges for the sustainability of tender boats is the emission of greenhouse gases. Many traditional tender boats are powered by internal combustion engines that use fossil fuels, such as diesel. However, significant progress has been made in the adoption of greener solutions in recent years.
One of the most promising alternatives is the use of electric motors. Electric tender boats are powered by rechargeable batteries, which eliminate direct greenhouse gas emissions. These boats can be powered by renewable energy sources, such as solar energy or hydroelectric energy, further contributing to the reduction of environmental impact.
Finally, sustainable tender boats can also adopt design practices that improve hydrodynamic efficiency, reducing water resistance and fuel consumption. The use of lightweight and resistant materials can help reduce the overall weight of the boat, further improving energy performance.
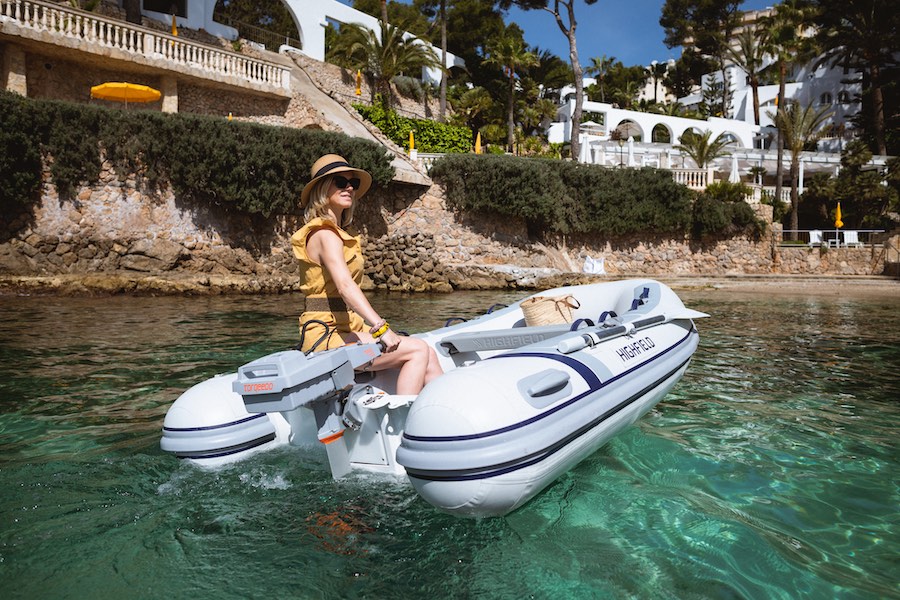
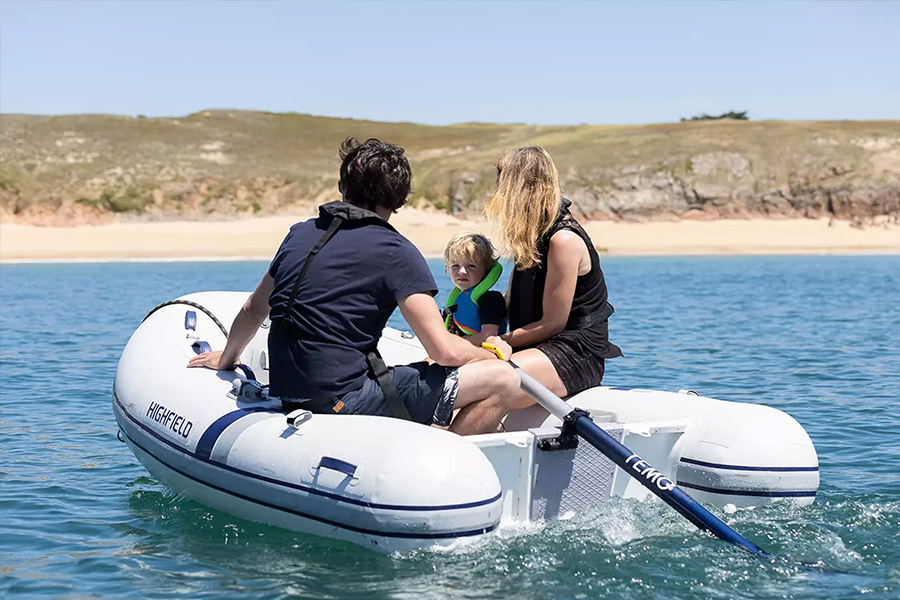
Regarding hydroelectric energy, and given the high importance of the issue of sustainability, we decided to develop the propeller for the electric motor of this type of boat.
The material selected for this type of application is the new UltiMaker PET CF, the first composite material in their portfolio specifically made to work perfectly with the UltiMaker S-series printers. Below is a brief description of the material characteristics:
- Its outstanding mechanical properties and resistance to chemicals and heat make it ideal for high-performance applications.
- Unlike other composite filaments, UltiMaker PET CF is not only available in black. It is also available in gray and blue, so as to also take into account the aesthetics of the finished product.
- With a flexural strength of ~100 MPa and a stiffness of ~6000 MPa, UltiMaker PET CF offers excellent mechanical properties.
- The material is fully integrated into the UltiMaker platform through NFC-equipped spools, a dedicated Print Core CC, support material compatibility, and print profiles.
Modeling and 3D printing
The propeller was modeled with the Autodesk Fusion 360 3D modeling software, much more than a CAD, as it is optimized for 3D printing. The 3D model was created by combining solid modeling with surface modeling. The result is shown in the next image.
The propeller was printed with an FFF printer such as the UltiMaker S5, a dual extruder printer that made it possible to print the PET CF with a water-soluble support material such as PVA. The choice of soluble support material is justified by the fact that the propeller has a blade thickness at the limit of printability, and this could be a reason for damage to the same when removing the support, also considering the curvature of the blade profile.
3D printing parameters we used:
- H=0.2mm
- Extrusion temperature=270°C;
- Top temperature=80°C;
- Print speed=30mm/s:
- Brim as a plate adherence;
- Infill=20%
- Wall line Count=2 --> 3
- Support Density=80% --> 50%
- Brim Width=7.0 --> 15.0mm
It is important to have an up-to-date version of the UltimMaker Cura slicing software (Version 5.4.0), as it contains updates and optimized profiles for PET CF.
The 3D printing result is truly remarkable. The material adhered perfectly to the printing surface, even without using glue for adhesion. The removal of the PVA support has made it possible to obtain a geometry with an exceptional aesthetic finish, also thanks to the right drying of the material to considerably reduce the amount of humidity absorbed.
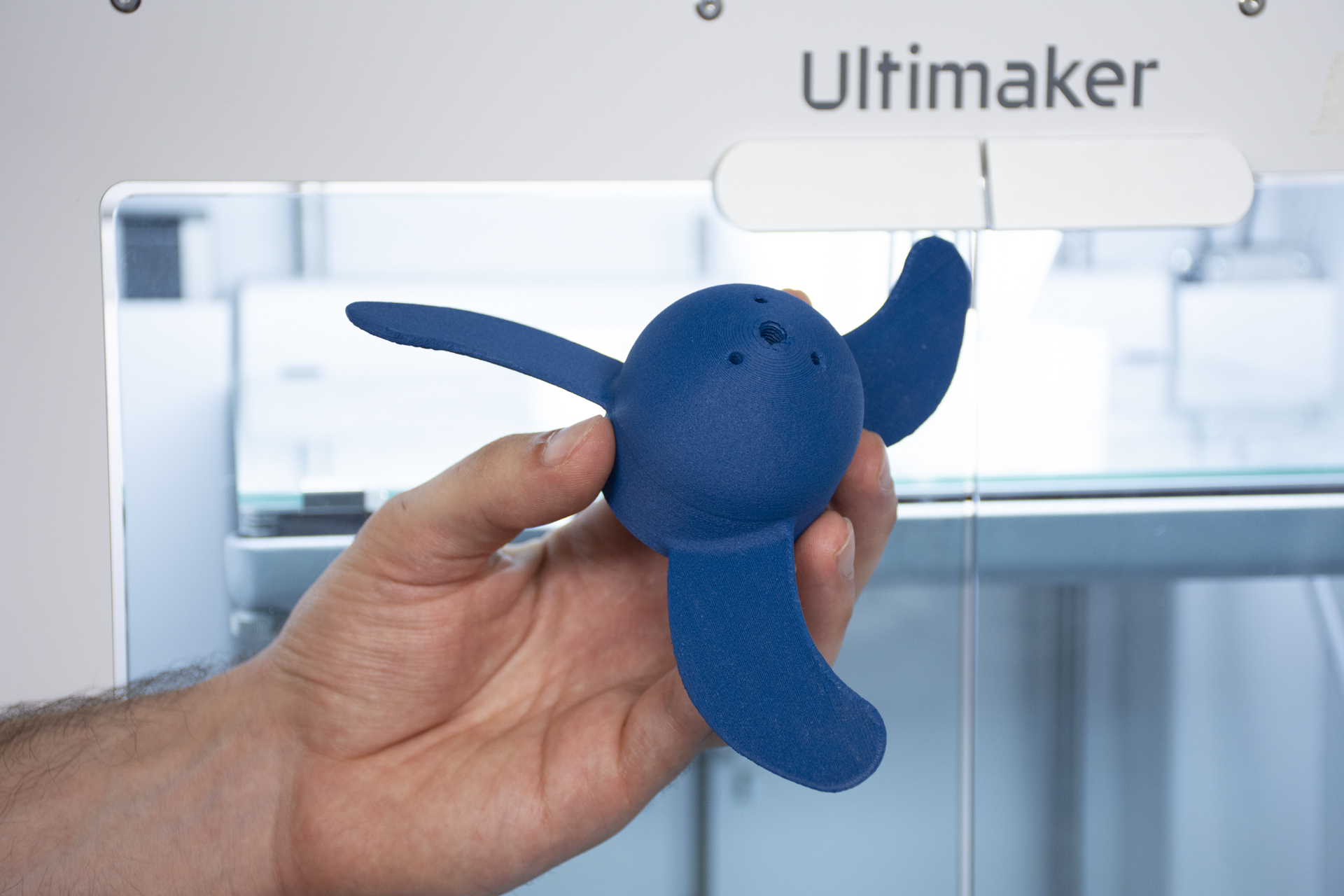
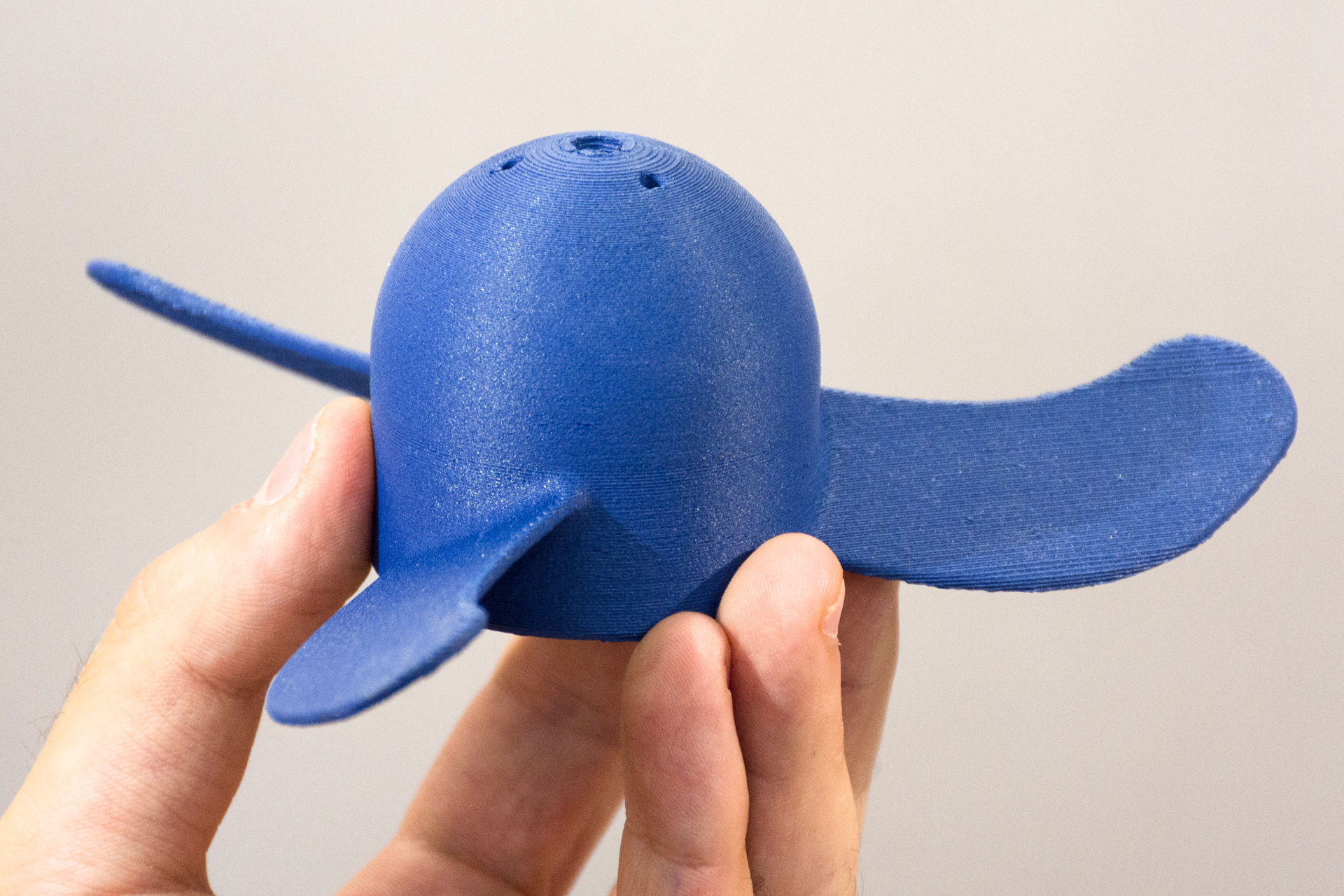
3D printing applied to this sector opens up numerous future scenarios, not only for tender-boats but also in other types, such as SUP, Flitescooter or Kayak.
In short, the market for these boats is enjoying such success as to increase enthusiasts and specific requests. And for this reason, manufacturing must also do its duty by offering designers a finished, sustainable product that respects requirements and purposes.