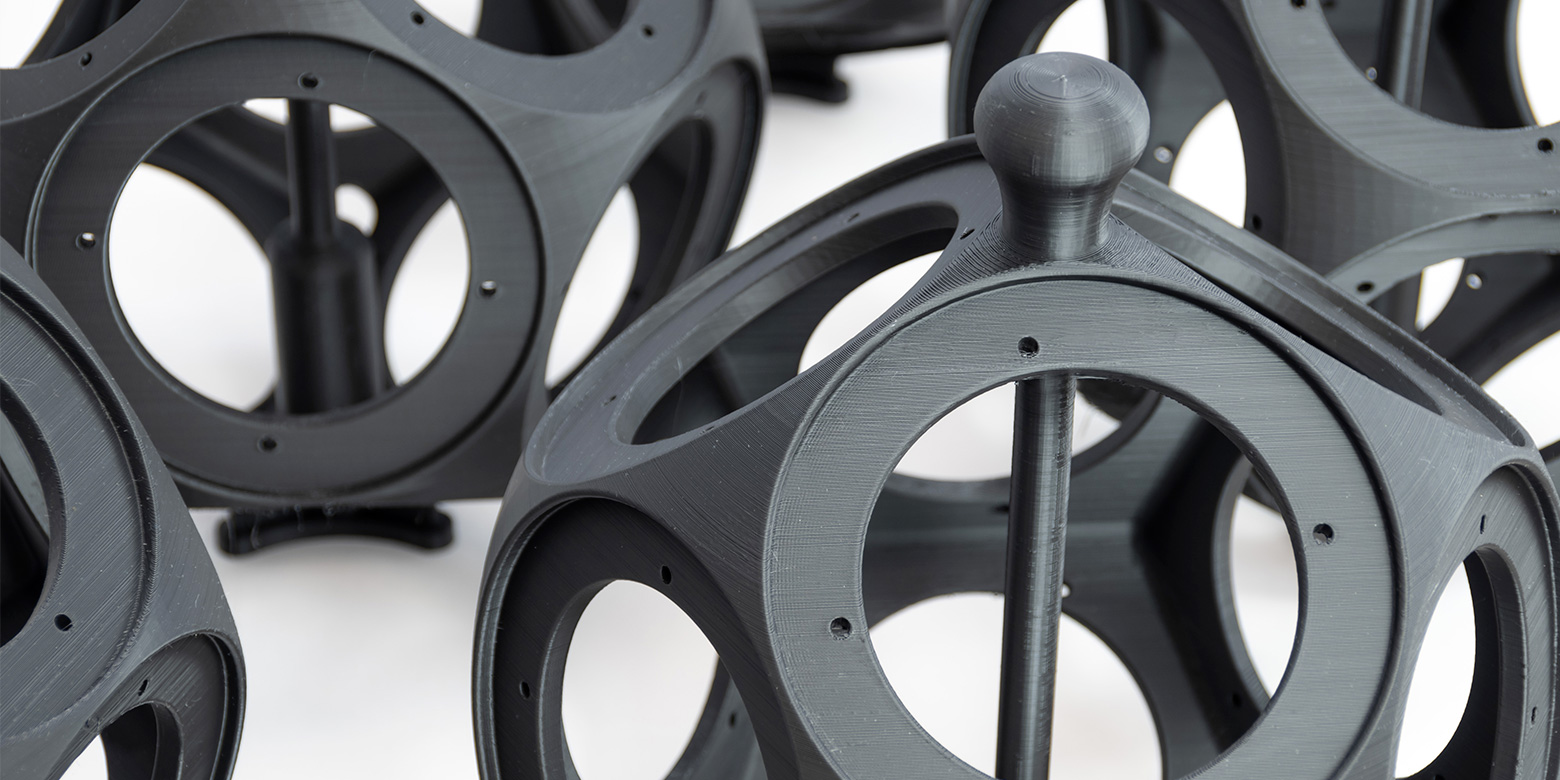
3D printing: NTEK new strength
NTEK is an Italian company specialized in products and services for the measurement and control of noise and the vibrations deriving from it, in all application fields of acoustics.
Within the range of proposed solutions, the dodecahedral sources of the OMNI series stand out, used to uniformly emit a sound in all directions, allowing correct measurement of insulation and reverberation time both in acoustics construction and architectural acoustics.
NTEK has recently revolutionized the production process of the Omni 4” Series by focusing on 3D printing, and entrusting the creation of the new products to Crea 3D, its technological partner also for the development of the design of the new dodecahedrons.
The 3D printing process
For the printing of the new Omni 4'', Crea 3D used the large format Raise3D printers, and the Fabbrix PLA HT filament.
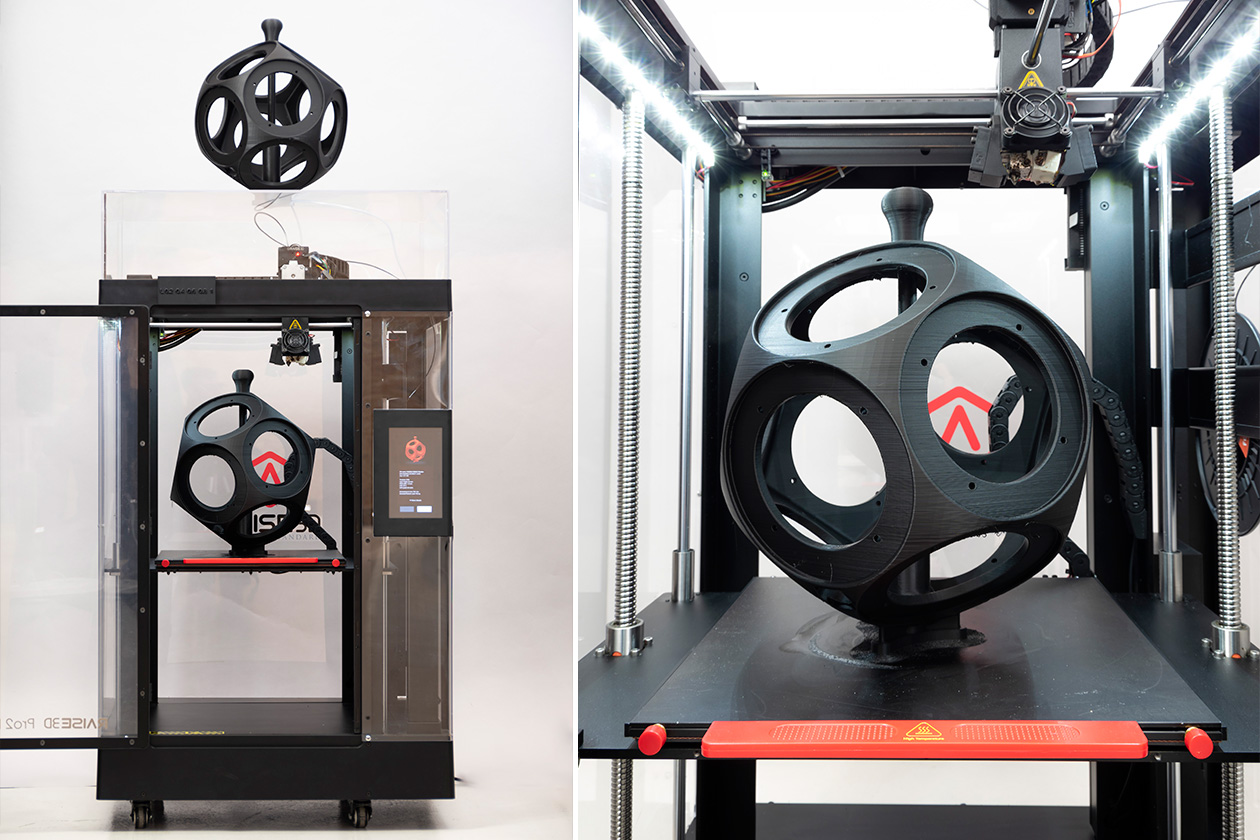
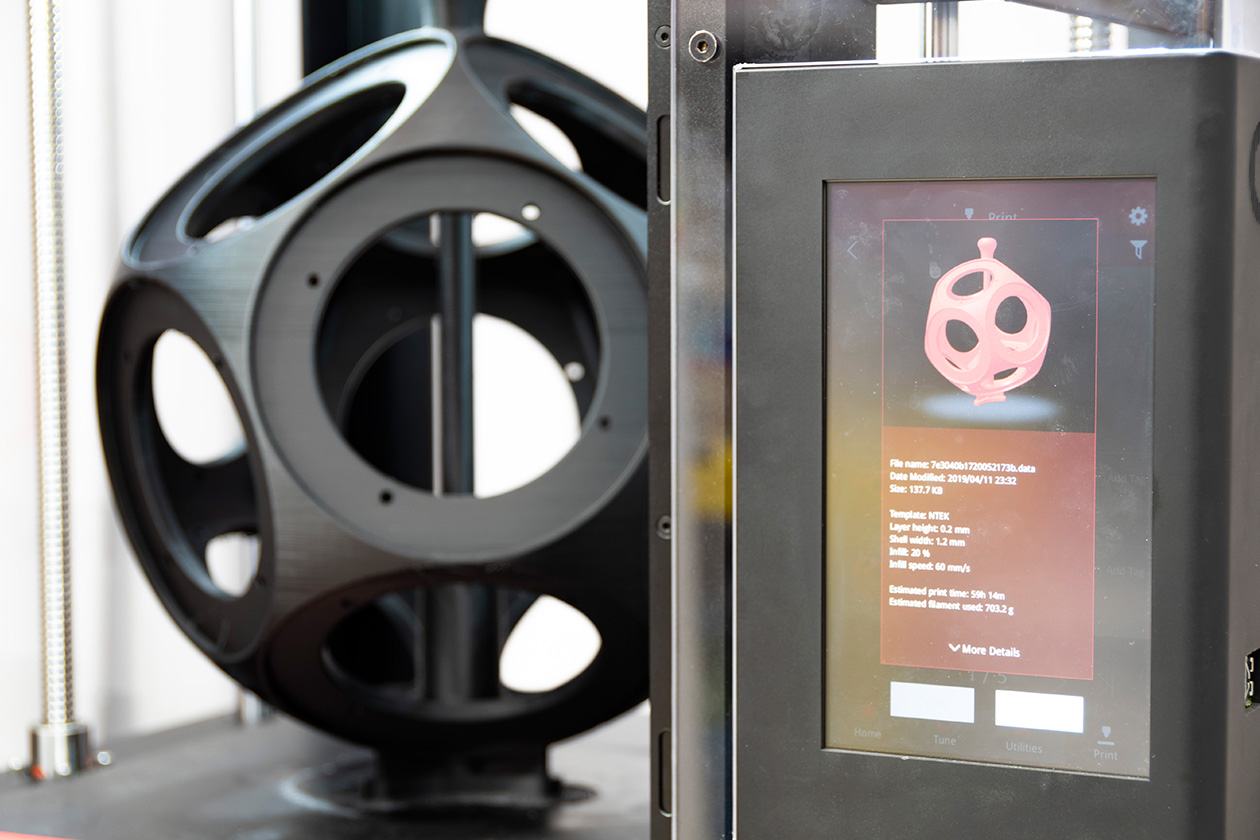
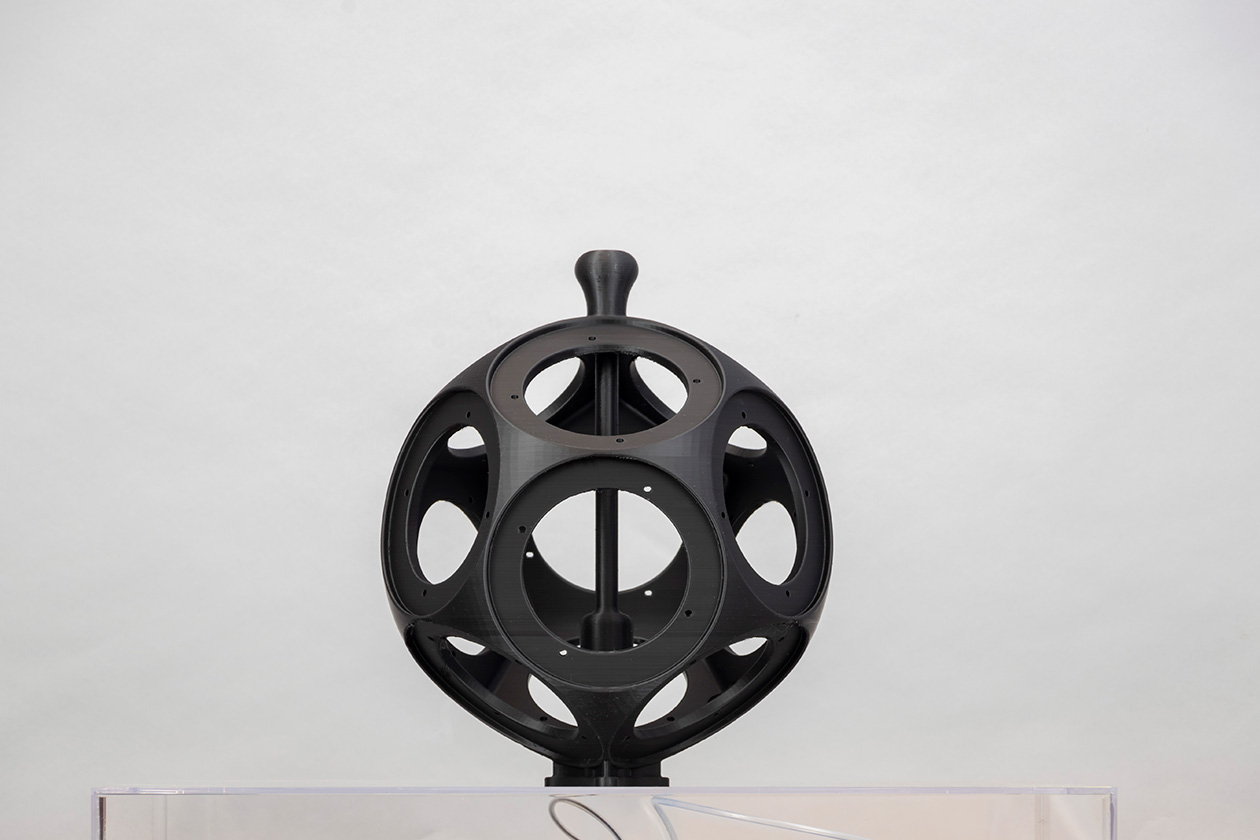
Benefits of 3D printing
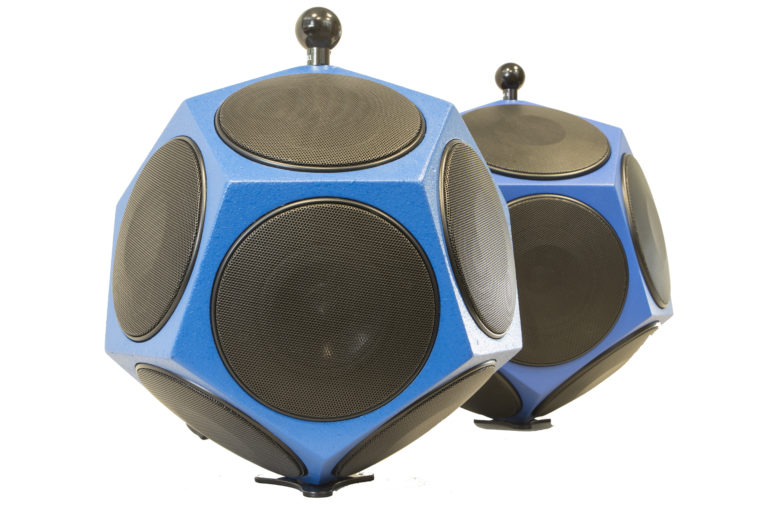
The traditional Omni 4” were made of wood (Finnish birch), which guaranteed excellent product performance.
The production, entrusted to an external supplier, required large quantities to amortize even the mold costs, with very long delivery times (a few months).
It was unthinkable to make changes during construction, even minimal ones, since they required the creation of a new mold, with additional costs and a considerable lengthening of delivery times.
The new 3D printed Omni 4” represent the real breakthrough. The production with additive technology, in addition to allowing greater freedom in the external design ensures, with its sphericity, the achievement of a greater isotropy and omnidirectionality.
3D printed with heat resistant material, they ensure excellent performance of the structure even after prolonged periods of activity, without incurring deformations due to the temperatures reached during operation.
Moreover:
- Designed according to needs and requirements, the new Omni 4” guarantees greater ergonomics: carrying by hand will be more comfortable given the new knob structure, which now ensures more comfortable and firm grip.
- The product is much lighter and more manageable than the traditional wooden version:
- OMNI 4 HP 3D printed: 7 Kg instead of 8.5 Kg
- OMNI 4 Lt 3D printed: 4,2 Kg instead of 5,5 Kg - The time saving, the possibility of printing even small quantities based on customer requests or market needs, and above all the possibility of carrying out changes in progress, prevail over the economic component.
“What was born from the beginning as a simple internal prototyping, in the name of new technologies, is now proving to be a remarkable workhorse. The first to adopt this new method: we feel proud to have invested and continue to invest in the field of new technologies and, where possible, make the most of them by directly modifying Ntek's production lines"
Giancarlo Sassi, NTEK General Manager